Fabricated Parts & Filters
From simple stamped screen packs to complex aviation fuel filters, wire mesh parts and filters play a key role in making day to day living seamless. Its pliable, precise, yet durable characteristics allows that material to be fabricated into to virtually an form factor.
This leaves your imagination as the only limit to what can be achieved with custom wire mesh fabrications.
W.S. Tyler has spent the past 150 years combing the technical expertise of our engineers, desingers, and craftsman with state-of-the-art manufacturing techniques to supply reliable and versatile wire mesh solutions. Whether apply wire mesh for filtration, separation, pretection, reniforment, or anywhere inbetween, we are ready to learn how your process works, help you develop revenue gerntatitng components, and serve as a subsidiary wire weaving division of your organization.
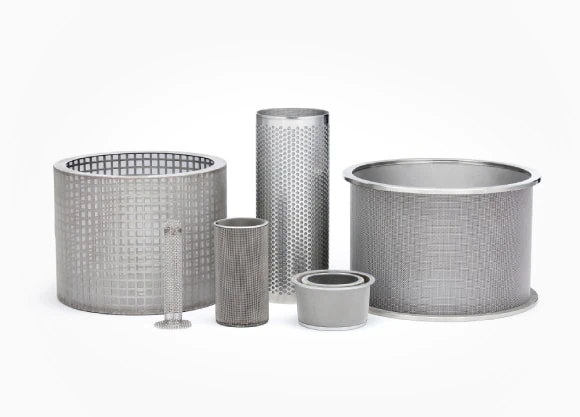
Take a Glimpse Into What’s Possible
Sintered Multilayered Wire Mesh
Woven wire mesh laminate consisting of multiple layers of wire mesh with variating specifications. These wire mesh layers are bonded using a specialize diffusion technique, ensuring the geometric profile of the mesh layers remain in tact.
Applications:
Gas filtration, high-capacity liquid filtration, chemical processing, pharmaceutical production, automotive filtration, aerospace filtration, and other separation and filtration applications.
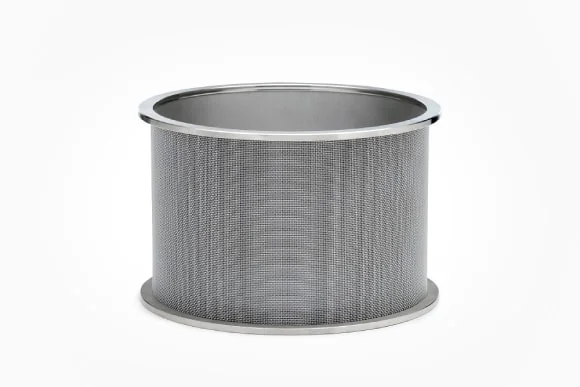
Section and Round Parts
Single- or multi-layer components fabricated using various cutting techniques. [RB1] These techniques include splitting, laser cutting, round cutting, stamping, and more.
Applications:
Extruder screens, chromatography, soil-catch screens, automotive components, other screen and filtration applications.
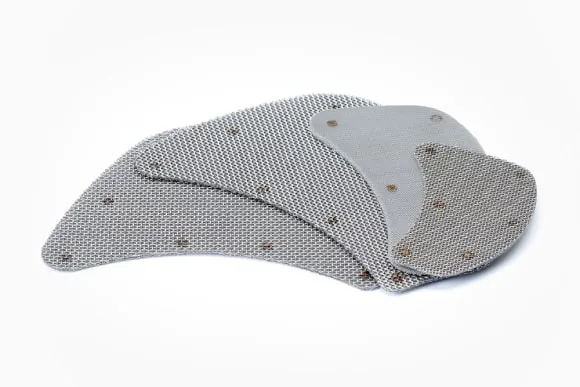
Inline Filter/Gasket Filters
Cylindrical wire mesh components affixed with a metal flange, designed to fit within sanitary pipe systems. While availbe instandard diameters of 1-inch, 2-inch, 2.5-inch, 3-inch, 4-inch, 6-inch, and 8-inch with a lengths spanning from 1.5 to 16 inches, inline filters can be customized to accommodate your needs.
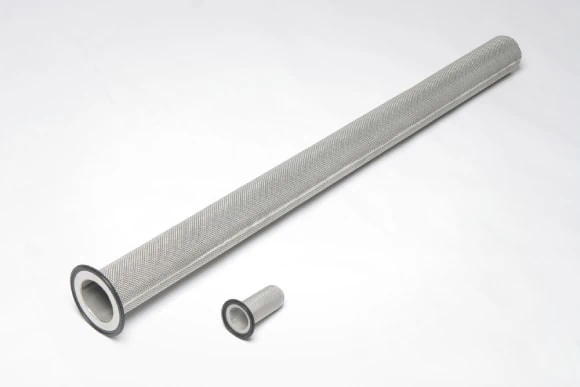
Cylindrical/Pleated Filter
Wire mesh filter components that take on a cylinder-like form after being joined at the longitudinal seam via specialized welding techniques. Furnished with either a smooth or pleated profile, supportive elements are added to each filter during fabrication.
Applications:
Water filtration, cooling fluid filtration, oil filtration, and other screening and filtration applications.
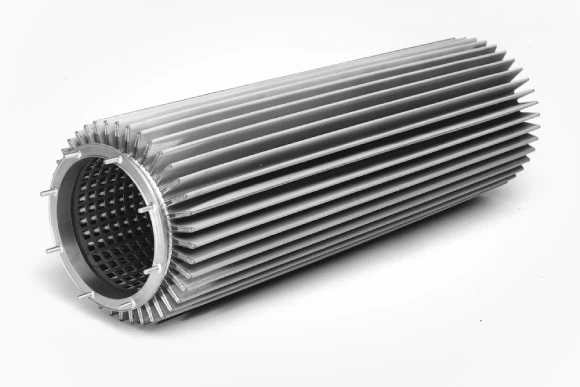
Filter Plates
Flat wire mesh plates put in place to remove particles within a specific particle size range from both liquids and gases. Designed for maximum durability and precision, help you achieve optimal results for prolonged periods of time.
Applications:
Wastewater filtration, pharmaceutical production, food and beverage production, chemical processing, liquid solid separation, and other separation and filtration applications
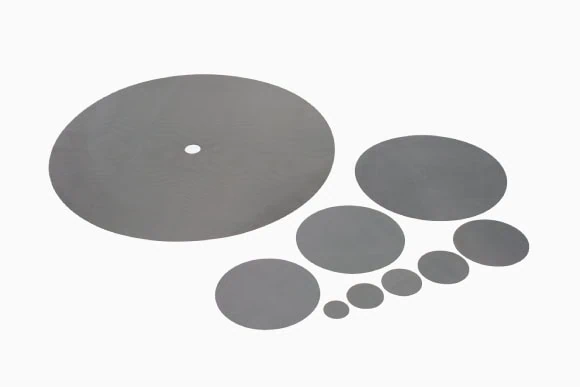
Need To Know
Lead Times
Industrial woven wire mesh lead times are heavily influenced by material availability, production scheduling, and the amount of value-added services you require. Typically we can ship mesh specifications that we have in-house within two business days.
That said, if your request is not within our facility but in stock with one of our suppliers, lead times would be around one to two weeks. Specialty wire mesh requests can sometimes reach lead times of 18 months.
To best manage your lead times you can do things such as request expedited shipping or place blanket orders.
Purchase Order
Industrial woven wire mesh lead times are heavily influenced by material availability, production scheduling, and the amount of added value services you require. Typically we can ship mesh specfitonats that we have in-house within two business days.
That said, if your request is not within our facility but in stock with one of our suppliers, lead times would be around one to two weeks. Specialty wire mesh requests can sometimes reach lead times of 18 months.
To best manage your lead times you can do things such as request expedited shipping or place blanket orders.
Your Mesh, Your Way
Value-Added Processes
Woven wire mesh is remarkably versatile off the loom, but sometimes it must be enhanced to deliver optimal performance. Our highly calculated and monitored value-added processes were designed to grant you complete control over the performance of your wire mesh.
Weave Type and Specifications
Dependable filtration and screening requires you to scientifically balance precision and flowrate. Get to know the different specifications and weave types you can use to fine-tune the performance of your wire mesh.
Alloys
Creating wire mesh solutions that deliver optimal durability, starts with the alloy of the wires. Explore our extensive wire mesh alloy selection and learn what it takes to fabricate solutions that perform under the harshest conditions.
Industries We Serve
Discover how woven wire rolls and cut-to-size pieces enable you to craft best-in-class solutions in-house while maintaining a reliable wire mesh inventory.
Aerospace Automotive Chromotography Pulp and Fiber Water Filtration Plastics and Extrusion Oil and Gas Carbon capture